Bosch ME9 ECU
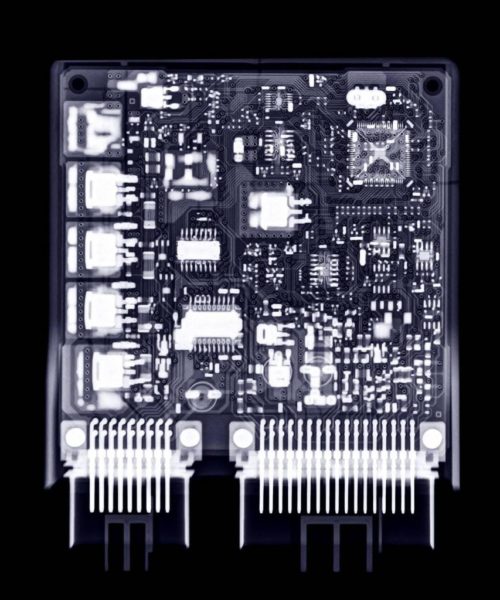
Bosch ME9 ECU
Bosch Montronic ME9
The Bosch ME9 Engine Control Unit (ECU) equipped in our vehicles is a testament to automotive innovation. Released nearly two decades ago, it was, at its time, one of the most advanced ECUs in the market, showcasing groundbreaking features such as a Torque-based Model system. This framework was particularly noteworthy for its ability to provide a more sophisticated and precise control over the engine performance, paving the way for enhanced driving dynamics and fuel efficiency.
This framework is based on a complex algorithm that continuously calculates and manages engine torque in real-time. It does so by accounting for various factors including throttle position, air intake, fuel mixture, and more. The ability to compute these different parameters and apply them instantaneously to the engine’s operation was a significant advancement in engine control technology at that time.
Bosch has made numerous revisions to the ME9 ECU over the years, refining its algorithms and enhancing its functionality. It has since been superseded by the ME17, and most recently, the MG1. Both of these newer versions have built upon the foundations of the ME9, incorporating even more advanced features and capabilities, such as enhanced fuel management systems and more robust diagnostics.
However, it’s worth noting that despite its age, the ME9 is far from obsolete. Certainly, there are newer ECUs now that boast more advanced Torque Modeling, yet the ME9 still holds its own when compared to these. With its pioneering chipset and robust build quality, the ME9 continues to deliver reliable and efficient performance, reflecting its enduring significance in the field of automotive engine control systems
Although the torque model is far more complex than how we portray it in this write-up, we will attempt to simplify it in consideration of this being a tuning course designed for beginners.
The Torque model of engine management is a form of “input/output” that the ECU (Engine Control Unit) can generate. To fully comprehend this, we need to delve into the past and examine the inner mechanics of older ECUs.
As vehicle engines became more complex due to additions like turbochargers, car manufacturers quickly recognized that the simple “EFI” (Electronic Fuel Injection) computer wasn’t up to the challenge. Given that most cars were also equipped with Electronic Ignition, it dawned on them that they would eventually need four or five separate computers to operate the vehicle. Consequently, they decided to develop a single, unified computer capable of handling all these tasks. Thus, the ECU was born.
The first iteration of the ECU uses the throttle plate angle as the basis for demand. This was to integrate the existing technology, which was the cable throttle body, into the ECU system. This is referred to as the “Basic Model“, named after the Motronic Basic.
The next iteration uses manifold air pressure as the basis for load demand. This system, dubbed the “Boost Model,” has been widely adopted by most manufacturers and has become the go-to ECU in the performance tuning scene. The process is simple: you map the throttle to the manifold pressure which directly controls the turbocharger. Let’s say it’s mapped in a linear fashion (which no one does, by the way), 100% of throttle will request maximum boost. A 50% throttle input gives you half of the maximum boost. The system is simple in design and functional in a sense, hence it remains very popular for turbo conversion builds, even today.
While this system “works,” the issue is that it doesn’t cope well with changes in barometric pressure. For example, let’s say you’ve set your maximum boost to 15psi at sea level; when you ascend to elevated areas, the density of air changes. If it’s capped at 15psi, your turbocharger has to work harder to achieve that 15psi, sometimes to the point of over-spooling. Additionally, the manner in which the engine burns the fuel-air mixture varies, so even if you attain that same amount of pressure, the engine’s performance may still feel sluggish.
To counter this, manufacturers began to factor in the air measured by an air meter (MAF) and adjusted their calculations based on Volumetric Efficiency. This is referred to as Load-based Modeling. Unlike the pressure model, this model calculates the amount of air filling the cylinders. With this system, boost varies depending on barometric pressure. The ECU targets a specific cylinder fill amount and bases its calculations on that. In this system, boost is not a constant pressure. If the ECU determines that it only needs 16psi of boost to achieve the requested load, it will only boost up to 16psi. If it decides that it needs 20psi, it will request 20psi. In this model, when a driver steps on the accelerator, they are technically requesting a certain amount of “load”. The ECU then performs the calculations and targets the requested psi and fueling. This system is already quite advanced in itself and should function as it is.
While the load-based model works most of the time, it is still somewhat primitive. The reason is that the Load = Power relationship is not static. For example, a 130% load may equate to 300NM of torque at 2500RPM, but it might only be 220NM at 3500RPM. Another area where it falls short is adjustability. Imagine, for instance, your vehicle is traveling at 80kph, at 3000RPM with an 80% load. You then encounter a hilly road that goes up and down. In this system, as long as the ECU is maintaining and targeting the 80% load, it’s doing its job. However, the torque required fluctuates depending on the inclination.
This is where the Torque-based modeling comes into play. In a Torque-based system, when you step on the accelerator, you are, in fact, requesting a certain percentage of the maximum attainable torque. The ECU then calculates how much load, fuel, ignition timing, VVT, etc., are needed to achieve the requested torque. Because of this, the torque model delegates most of the functions to the ECU. Most drive-by-wire vehicles follow the Torque model, though there are exceptions. In essence, the only direct control the driver now has is over the accelerator.
To sum up, anyone familiar with the quirks of older cars can appreciate the substantial upgrade this system represents. Where older cars struggled and strained against inclines, the modern torque-based model takes such challenges in stride. It’s a system that auto-adjusts, that reads and understands the needs of the driver and the demands of the environment. It then calculates the most efficient route to delivering the necessary power, smoothing out the uphill battles of the past. This is the beauty of evolution in automotive technology – the continuous push towards more powerful, efficient, and intuitive driving experiences. As we conclude, we realize that while we journey through the intricate world of engine tuning, the most exciting part is witnessing how far we’ve come, and imagining the possibilities of where we’re headed.